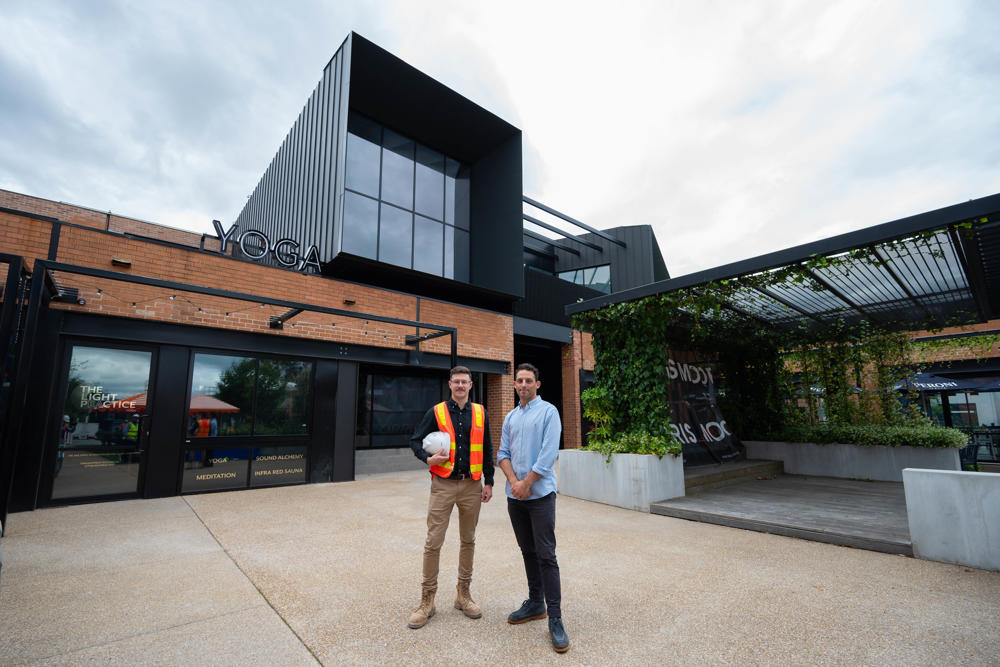
The 1960s industrial precinct formerly owned by Philip Morris has been sustainably transformed into a $200 million commercial community, the adaptive reuse process included the retainment of the existing structure throughout the build.
This has resulted in savings to date of 19 million kilograms of embodied carbon — which is the equivalent of 400 rail cars full of coal.
After the completion of Building 4, the project’s builder — Kapitol Group — delivered a construction program in which these embodied carbon savings contributed to the developer’s overall goal for the site to increase energy efficiency and reduce operating costs.
This was further supported by sustainable onsite infrastructure, including a 460 solar panel system which will generate up to 245 kWp.
Kapitol Group Project Manager Jamie Kerr has led the delivery of Building 4 and confirmed the growing demand for efficient community-focused developments.
“Customers are becoming increasingly aware of the environmental impacts of development and are specifically looking for sustainable options.
“Adaptive reuse presents a great opportunity in this space,” said Kerr.
With the built environment contributing 37 per cent to global greenhouse gas emissions, the entire property industry’s focus has begun to shift towards major ESG initiatives, striving towards a more sustainable future for the industry and the wider community.
Morris Moor is a key example of adaptive reuse, through the retention and reuse of the existing buildings in their entirety
The Green Building Council recently released data indicating that 42 per cent of the upfront carbon of a building is within the superstructure, 13 per cent in the substructure and 15 per cent within the envelope, including the façade and roof.
Being able to retain these assets throughout the build of Morris Moor allowed for a significant reduction in embodied carbon.
As part of the demolition program, Kapitol Group was able to achieve a 92 per cent recycled rate of materials.
In order to work with the existing infrastructure, Kapitol Group undertook careful hand demolition of the existing structure.
Kerr confirmed that “partial demolition of an existing structure in a live environment is both complex and time-consuming”.
“However, this careful process has allowed us to salvage materials such as the original façade brickwork which has been re-purposed throughout the building.
“A careful and considered approach to demolition and temporary works is essential for working around existing conditions and ensuring sustainability outcomes are achieved,” said Kerr.
Spanning 6.3 hectares, the project has been led by Up Property, who appointed impact architects, ClarkeHopkinsClarke, and Kapitol Group for building four.
Morris Moor has been devised to appeal to growing businesses, with the likes of New Balance relocating its Australian headquarters to the site, which is already home to well-known hospitality operators such as Stomping Ground Brewery, and Holey Moley.
Up Property General Manager Marcus Jankie says the adaptation of what was once Moorabbin’s major employer has had a widespread impact, directly from the 19 million kg of embodied carbon savings.
Jankie explained: “It would take more than 7,500 hectares or 4,300 MCG ovals full of eucalyptus forest to absorb that amount of carbon over the course of an entire year.”
When discussing the mission and focus of Up Property’s refurbishment of these iconic buildings, Jankie confirmed that “the goal was to reuse as much of the existing building as possible.
“This involved retaining the structure, finishes, flooring and glazing to not only capture the invaluable and non-replicable charter of the buildings but to harness the one-off opportunity of limited environmental impact through adaptive reuse over new construction.
“This was maximised not only through thoughtful design by the consultant team but executed practically by an experienced builder — Kapitol Group.”
Architect and Associate at ClarkeHopkinsClarke Gaston Nogues said that it’s an approach now driving the best placemaking worldwide.
“Adaptive reuse is great because it breathes new life into unique places, minimises embodied carbon, reduces operational carbon and construction waste, and makes construction quicker and more cost-effective,” said Nogues.